Introduction: The Rise of Electric Vehicles and the Supply Chain Demands
The rapid rise of electric vehicles (EVs) is transforming the global automotive industry. With increasing government regulations promoting cleaner emissions, advancements in battery technology, and a growing consumer demand for more sustainable transportation options, the electric vehicle market has gained significant traction. However, as the demand for EVs skyrockets, there is an urgent need to assess whether the existing supply chains can meet these demands.
The electric vehicle supply chain is multifaceted, with critical components such as batteries, raw materials, semiconductors, and energy infrastructure playing pivotal roles. As automakers and new startups ramp up EV production to meet both consumer expectations and regulatory targets, they must overcome significant supply chain challenges. These challenges, however, also bring about numerous opportunities for innovation and expansion in the industry. In this article, we will evaluate the current state of the EV supply chain, identify its key challenges, and explore the opportunities that lie ahead for the industry.
Understanding the EV Supply Chain: Key Components
The electric vehicle supply chain is fundamentally different from that of traditional internal combustion engine (ICE) vehicles due to the distinct components involved in the manufacturing of EVs. Understanding the key elements that make up the EV supply chain is essential to assessing its readiness for growing demand.
1. Battery Production
Arguably, the most important component of the EV supply chain is the battery. Electric vehicles rely on large lithium-ion batteries to power their electric motors. The quality, performance, and cost of these batteries directly influence the affordability and appeal of EVs. As a result, the EV battery supply chain has become the focal point of the electric vehicle revolution.
Currently, most EV manufacturers source their batteries from a few key players, such as LG Chem, Panasonic, and CATL. However, with the surging demand for EVs, automakers are facing significant pressure to secure a stable and scalable supply of high-quality batteries. Battery shortages, rising raw material costs, and concerns over ethical mining practices for essential minerals like lithium, cobalt, and nickel have highlighted vulnerabilities in the battery supply chain. The long-term sustainability of the EV supply chain will depend heavily on innovations in battery technology and the development of secure, ethical sources of raw materials.
2. Raw Materials
The production of batteries is dependent on a range of raw materials, including lithium, cobalt, nickel, graphite, and rare earth elements. The growing demand for these materials has put significant pressure on global supply chains, driving up costs and raising concerns over resource scarcity.
For instance, cobalt, which is used in the production of lithium-ion batteries, has been the subject of considerable ethical debates, as much of the global supply comes from the Democratic Republic of Congo, where mining practices are often criticized for their environmental and human rights impacts. Similarly, nickel and lithium—essential for producing high-capacity batteries—are facing supply constraints, and global production is struggling to keep up with demand.
These challenges have sparked a drive for innovation in material sourcing, recycling, and battery chemistry, with companies exploring ways to reduce reliance on certain critical materials and improve the recyclability of batteries.
3. Semiconductor Chips
Semiconductors play an essential role in EVs, powering everything from the vehicle’s infotainment system to its autonomous driving capabilities. The global semiconductor shortage, which has affected various industries since 2020, has been a significant challenge for the automotive sector, including electric vehicle manufacturers. In particular, the rise of smart vehicles, which rely on advanced microchips, has put added pressure on the semiconductor supply chain.
Semiconductor shortages have led to production delays and increased vehicle prices, highlighting the need for a more robust and resilient semiconductor supply chain in the EV market. With governments and industry players recognizing the strategic importance of semiconductor manufacturing, there is growing investment in establishing new chip production facilities and securing stable supply chains for the EV market.
4. Charging Infrastructure
One of the most critical factors for the widespread adoption of electric vehicles is the availability of charging infrastructure. EVs are only as practical as the ability to charge them, and this requires a robust network of public and private charging stations. The charging infrastructure supply chain encompasses the production and installation of charging stations, electrical grid capacity, and energy storage systems.
As EV adoption grows, so does the need for more charging stations. Traditional automakers, as well as new entrants like Tesla, have been expanding their charging networks, but significant challenges remain, including the high costs of infrastructure, the uneven distribution of charging stations across regions, and the integration of renewable energy sources into the charging network.
To address these challenges, there is a growing focus on expanding fast-charging networks, improving the efficiency of charging technology, and ensuring equitable access to charging stations in urban and rural areas alike.
5. Vehicle Production and Supply Chain Resilience
Aside from components like batteries and semiconductors, the vehicle manufacturing process itself involves various suppliers and components, such as electric motors, power electronics, and vehicle chassis. Traditional automakers are investing heavily in electric vehicle production lines, retooling existing factories, and developing new facilities designed specifically for EVs.
Supply chain resilience is a key issue here, as many automakers rely on a global network of suppliers for parts and components. However, disruptions—whether from geopolitical instability, trade conflicts, or the COVID-19 pandemic—have exposed the fragility of the global supply chain. In the EV space, automakers must find ways to ensure continuity and mitigate risks, such as sourcing parts locally, diversifying suppliers, and employing advanced digital supply chain tools to monitor and optimize production.
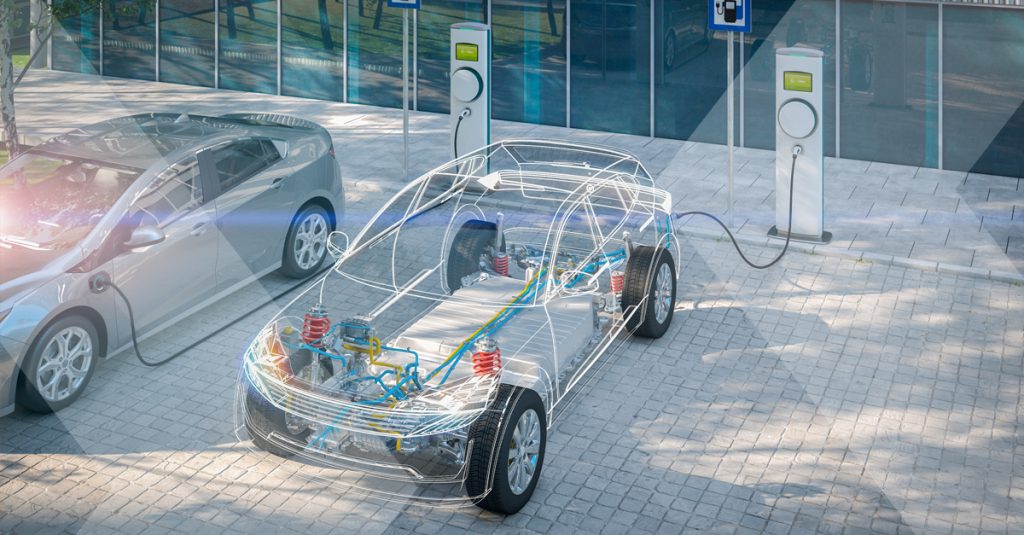
Challenges in the EV Supply Chain
Despite its significant potential, the EV supply chain faces several challenges that must be addressed if it is to meet growing demand. These challenges span technological, logistical, geopolitical, and environmental issues, all of which require innovative solutions to ensure the EV supply chain can support the future of electric mobility.
1. Raw Material Shortages and Price Volatility
As mentioned earlier, the raw materials required for battery production are facing supply constraints, leading to price volatility. The mining of lithium, cobalt, nickel, and other materials essential for EV batteries presents both logistical challenges and ethical concerns. Given the rising demand for these materials, securing stable, long-term supply agreements is crucial. Moreover, mining practices must become more sustainable to avoid environmental damage and human rights violations.
Automakers and battery manufacturers are responding by seeking alternative sources of raw materials, such as recycling and extracting materials from used batteries, and investing in research to create alternative battery chemistries that rely on more abundant or less controversial materials.
2. Dependency on Limited Battery Suppliers
Currently, the global market for EV batteries is concentrated in the hands of a few major suppliers. This limited number of suppliers puts the industry at risk of bottlenecks and supply chain disruptions. Additionally, this reliance on a small number of battery producers means that any instability in the battery supply chain could lead to delays in EV production.
To mitigate this risk, automakers are working to diversify their battery supply chains, with some companies like Tesla and Volkswagen even investing in building their own battery factories. This trend is part of a broader strategy to reduce dependency on external suppliers and create more control over their supply chains.
3. Lack of Charging Infrastructure
Although the availability of charging stations has improved in recent years, the infrastructure is still insufficient to meet the needs of a rapidly growing fleet of EVs. Consumers in many regions remain concerned about range anxiety and the accessibility of charging stations, particularly in rural or underserved areas.
Building a robust, fast-charging network requires massive investments in infrastructure and energy systems. Furthermore, governments and private sector players must collaborate to ensure that the network is scalable and efficient, with a focus on integrating renewable energy sources into the grid to further reduce the carbon footprint of electric mobility.
4. Geopolitical Instability
Geopolitical tensions, particularly in regions where raw materials for batteries are sourced, can disrupt supply chains and create uncertainties in the global market. For example, the Democratic Republic of Congo, which supplies a significant proportion of the world’s cobalt, is known for political instability and human rights issues.
Automakers and governments must find ways to ensure that the materials required for EV production are sourced responsibly and ethically, which may involve diversifying supply chains or investing in new technologies to reduce reliance on certain materials.
Opportunities in the EV Supply Chain
While the challenges in the EV supply chain are significant, there are numerous opportunities to be seized. These opportunities lie in innovation, strategic partnerships, and government support, all of which can help overcome obstacles and build a more sustainable, resilient EV supply chain.
1. Battery Recycling and Second-Life Applications
Battery recycling is emerging as a critical solution to address raw material shortages. By recycling used EV batteries, manufacturers can recover valuable materials such as lithium, cobalt, and nickel, reducing the need for mining. Furthermore, repurposing old EV batteries for second-life applications, such as energy storage systems, can help extend their usefulness and reduce waste.
Governments and companies alike are investing in battery recycling infrastructure, creating new business models and job opportunities. Advances in recycling technology will also drive down costs and improve the overall sustainability of the EV supply chain.
2. Localized Manufacturing and Supply Chain Diversification
One of the key strategies to increase supply chain resilience is to localize manufacturing and diversify suppliers. By sourcing materials and components closer to home, automakers can reduce their dependence on distant suppliers and mitigate risks associated with global supply chain disruptions.
Several automakers have already begun building new factories for EV production and batteries in strategic locations around the world. This trend is expected to continue, with an emphasis on creating localized supply chains that are more flexible and less vulnerable to geopolitical risks.
3. Collaborative Partnerships
The challenges facing the EV supply chain are vast, but they also present an opportunity for collaboration across industries. Automakers, technology companies, governments, and energy providers can work together to build the necessary infrastructure and supply chain networks for electric vehicles.
Collaborative partnerships could also focus on developing innovative technologies, such as next-generation batteries, charging solutions, and renewable energy integration. By combining expertise and resources, stakeholders can drive the transformation of the EV supply chain and make electric vehicles more accessible to a global audience.
Conclusion: A Resilient and Growing EV Supply Chain
The electric vehicle supply chain is at a crossroads, with significant challenges that must be overcome to meet growing demand. However, these challenges also present opportunities for innovation, strategic partnerships, and the development of more sustainable and resilient supply chains. The EV industry is rapidly evolving, and as automakers, suppliers, and governments invest in new technologies and infrastructure, the future of electric vehicles looks promising.
The readiness of the EV supply chain for prime time will depend on how effectively the industry addresses issues such as raw material shortages, battery production, charging infrastructure, and geopolitical risks. With the right investments, collaboration, and innovation, the EV supply chain has the potential to meet the demands of the electric mobility revolution and help drive a more sustainable future for transportation.