1. Introduction
The global push toward electric vehicles (EVs) is driven by the need to reduce greenhouse gas emissions and dependence on fossil fuels. However, the energy efficiency of EVs remains a critical factor in their widespread adoption. One promising avenue for improving efficiency is the use of lightweight materials, which can reduce vehicle weight and enhance performance. This article examines whether the large-scale application of lightweight materials can significantly boost EV energy efficiency, analyzing the benefits, challenges, and future potential of these advanced materials.
2. The Importance of Lightweight Materials in EVs
2.1 Weight and Energy Efficiency
- Energy Consumption: Reducing vehicle weight directly decreases the energy required for acceleration and maintaining speed.
- Range Extension: Lighter EVs can travel farther on a single charge, addressing range anxiety.
2.2 Current Challenges in EV Design
- Battery Weight: EV batteries are heavy, often accounting for 25-30% of total vehicle weight.
- Performance Trade-offs: Balancing weight reduction with safety, durability, and cost.
2.3 The Role of Lightweight Materials
- Material Substitution: Replacing traditional steel and aluminum with lighter alternatives.
- Design Optimization: Integrating lightweight materials into vehicle architecture for maximum efficiency.
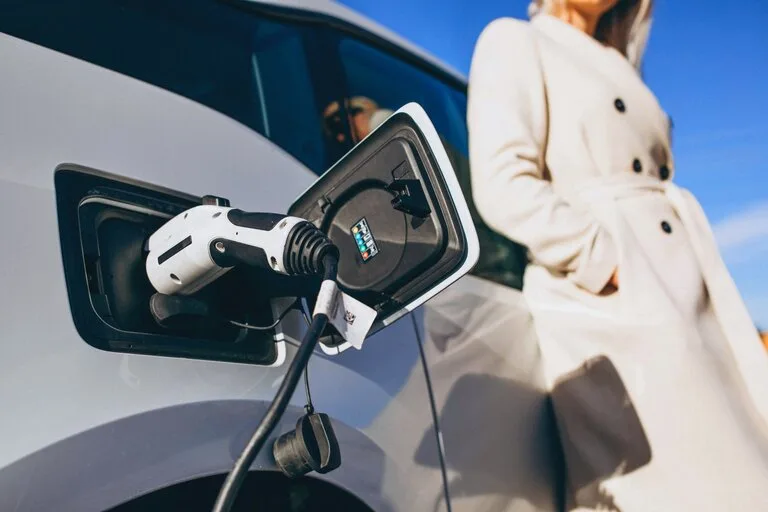
3. Types of Lightweight Materials
3.1 Advanced High-Strength Steels (AHSS)
- Properties: High strength-to-weight ratio, improved crash performance.
- Applications: Body structures, safety components.
3.2 Aluminum Alloys
- Properties: Lightweight, corrosion-resistant, recyclable.
- Applications: Body panels, chassis components.
3.3 Magnesium Alloys
- Properties: Extremely lightweight, good mechanical properties.
- Applications: Seat frames, steering wheels.
3.4 Carbon Fiber Reinforced Polymers (CFRP)
- Properties: Exceptional strength and stiffness, very lightweight.
- Applications: High-performance vehicles, luxury EVs.
3.5 Composites and Hybrid Materials
- Properties: Tailored properties for specific applications.
- Applications: Structural components, interior parts.
4. Benefits of Lightweight Materials in EVs
4.1 Improved Energy Efficiency
- Reduced Energy Consumption: Lighter vehicles require less energy to move, improving overall efficiency.
- Extended Range: Weight reduction can increase EV range by 5-10%.
4.2 Enhanced Performance
- Acceleration: Lower weight improves acceleration and handling.
- Braking: Reduced mass decreases braking distance and wear on brake components.
4.3 Environmental Impact
- Lower Emissions: Improved efficiency reduces the carbon footprint of EVs.
- Recyclability: Many lightweight materials, such as aluminum and composites, are recyclable.
4.4 Cost Savings
- Battery Size Reduction: Lighter vehicles can achieve the same range with smaller batteries, lowering costs.
- Operational Savings: Reduced energy consumption translates to lower charging costs.
5. Challenges in Adopting Lightweight Materials
5.1 High Costs
- Material Costs: Lightweight materials like carbon fiber are expensive compared to traditional materials.
- Manufacturing Costs: Advanced manufacturing techniques (e.g., autoclave curing for CFRP) increase production costs.
5.2 Manufacturing Complexity
- Processing Challenges: Lightweight materials often require specialized equipment and processes.
- Integration Issues: Combining different materials in a single vehicle can be complex.
5.3 Durability and Safety
- Crash Performance: Ensuring lightweight materials meet safety standards is critical.
- Long-Term Durability: Resistance to fatigue, corrosion, and environmental factors must be addressed.
5.4 Supply Chain and Recycling
- Material Availability: Ensuring a stable supply of lightweight materials is a challenge.
- Recycling Infrastructure: Developing efficient recycling methods for composites and hybrid materials.
6. Case Studies: Lightweight Materials in Action
6.1 Tesla Model 3
- Aluminum and Steel Mix: Uses a combination of aluminum and high-strength steel to balance weight and cost.
- Efficiency Gains: Achieves a range of 353 miles on a single charge.
6.2 BMW i3
- Carbon Fiber Reinforced Plastic (CFRP): Extensive use of CFRP in the body structure.
- Weight Reduction: Weighs 1,195 kg, significantly lighter than comparable EVs.
6.3 Jaguar I-PACE
- Aluminum Intensive: Aluminum body and chassis reduce weight while maintaining strength.
- Performance: Delivers a range of 292 miles with excellent acceleration.
7. Future Projections and Innovations
7.1 Material Advancements
- Next-Gen Composites: Development of cheaper, more sustainable composites.
- Nanomaterials: Incorporation of nanotechnology for enhanced properties.
7.2 Manufacturing Innovations
- Additive Manufacturing: 3D printing for lightweight, complex components.
- Automated Production: Robotics and AI for efficient material processing.
7.3 Policy and Industry Trends
- Regulatory Push: Stricter emissions standards driving lightweight adoption.
- Industry Collaboration: Partnerships between automakers and material suppliers to accelerate innovation.
8. Conclusion: The Path to a Lighter, More Efficient Future
The large-scale application of lightweight materials holds immense potential for significantly improving the energy efficiency of electric vehicles. While challenges such as high costs and manufacturing complexity remain, ongoing advancements in materials science and production technologies are paving the way for broader adoption. As the automotive industry continues to innovate, lightweight materials will play a crucial role in creating a more sustainable and efficient future for transportation. In the words of Elon Musk, “The future of transportation is not just electric—it’s lightweight, efficient, and sustainable.”