Compare the Technological Advancements in Electric Vehicles with Those of Traditional Internal Combustion Engine Vehicles
The automotive industry is undergoing a seismic shift as electric vehicles (EVs) challenge the dominance of traditional internal combustion engine (ICE) vehicles. This transformation is not just about replacing gasoline engines with batteries; it’s a complete reimagining of vehicle design, performance, and functionality. While ICE vehicles have been the backbone of the automotive industry for over a century, EVs are pushing the boundaries of innovation with advancements in battery technology, software integration, and autonomous driving. For traditional automakers, keeping up with these rapid technological advancements is both a challenge and an opportunity. In this article, we’ll compare the technological advancements in EVs with those of ICE vehicles, examine how these changes are impacting traditional manufacturers and supply chains, and explore the competitive dynamics shaping the future of the automotive industry.
Industry Impact: Examine How Electric Vehicles Impact Traditional Manufacturers and Supply Chains, Highlighting Industry Changes and Competitive Dynamics
The Evolution of ICE Vehicles: A Century of Incremental Improvements
Internal combustion engine vehicles have been the dominant mode of transportation for over a century, with continuous improvements in performance, efficiency, and safety. The technological advancements in ICE vehicles have been largely incremental, focusing on optimizing engine performance, reducing emissions, and enhancing fuel efficiency. For example, advancements in turbocharging, direct fuel injection, and variable valve timing have significantly improved the power and efficiency of ICE engines. Similarly, the development of hybrid vehicles, which combine ICE engines with electric motors, has further enhanced fuel efficiency and reduced emissions.
However, despite these advancements, ICE vehicles are fundamentally limited by the physics of combustion engines. The efficiency of ICE engines is constrained by the Carnot cycle, which limits the amount of energy that can be converted into useful work. As a result, even the most advanced ICE engines are significantly less efficient than electric motors, which convert a higher percentage of energy into motion. Additionally, ICE vehicles produce harmful emissions, such as carbon dioxide (CO2), nitrogen oxides (NOx), and particulate matter, which contribute to air pollution and climate change.
The Rise of Electric Vehicles: A New Era of Innovation
Electric vehicles represent a paradigm shift in automotive technology, offering a clean, efficient, and high-performance alternative to ICE vehicles. The technological advancements in EVs are driven by innovations in battery technology, electric drivetrains, and software integration, which are redefining the capabilities and functionality of vehicles.
Battery Technology: The Heart of EV Innovation
Battery technology is the cornerstone of EV innovation, and it has seen remarkable advancements in recent years. Lithium-ion batteries, which are the most common type of EV battery, have become more energy-dense, affordable, and durable. The energy density of lithium-ion batteries has increased significantly, enabling EVs to achieve longer ranges on a single charge. For example, the Tesla Model S Long Range can travel over 400 miles on a single charge, while the Lucid Air boasts a range of over 500 miles.
In addition to lithium-ion batteries, new battery technologies are emerging that promise even greater performance and sustainability. Solid-state batteries, which use solid electrolytes instead of liquid ones, offer higher energy density, faster charging times, and improved safety. Companies like Toyota and QuantumScape are leading the way in developing solid-state batteries, with the potential to revolutionize the EV industry.
Electric Drivetrains: Simplicity and Performance
Electric drivetrains are another area where EVs have a significant advantage over ICE vehicles. Unlike ICE engines, which have hundreds of moving parts, electric drivetrains are relatively simple, consisting of an electric motor, a single-speed transmission, and a battery pack. This simplicity not only reduces maintenance costs but also enhances performance. Electric motors deliver instant torque, providing rapid acceleration and a smooth driving experience. For example, the Tesla Model S Plaid can accelerate from 0 to 60 mph in under 2 seconds, making it one of the fastest production cars in the world.
Software Integration: The Future of Mobility
Software integration is a key differentiator for EVs, enabling advanced features like over-the-air (OTA) updates, autonomous driving, and connected car services. Tesla, in particular, has set a high bar for software integration, with its vehicles receiving regular OTA updates that enhance performance, add new features, and improve safety. For example, Tesla’s Full Self-Driving (FSD) package includes features like Autopilot, which can handle highway driving, and Navigate on Autopilot, which can automatically change lanes and navigate interchanges.
Other automakers are also investing in software integration to enhance the functionality and user experience of their EVs. For example, Volkswagen’s ID series of electric vehicles features a digital cockpit with a customizable display, while Ford’s Mustang Mach-E offers a large touchscreen with intuitive controls and seamless smartphone integration.
The Impact of EV Innovation on Traditional Manufacturers
The rapid pace of EV innovation is forcing traditional automakers to rethink their strategies and accelerate their transition to electric mobility. For many automakers, this transition represents a significant challenge, as it requires substantial investment in new technologies, manufacturing processes, and supply chains. However, it also offers an opportunity to redefine their role in the automotive industry and capture a share of the rapidly growing EV market.
Supply Chain Disruption: Adapting to New Requirements
The shift to electric vehicles is disrupting traditional supply chains, forcing automakers and suppliers to adapt to new requirements and challenges. Unlike ICE vehicles, which rely on complex mechanical systems and thousands of moving parts, EVs are built around simpler electric drivetrains and battery packs. This shift is disrupting traditional supply chains, as automakers and suppliers adapt to the new requirements of EV production.
For example, the production of ICE vehicles relies heavily on components like engines, transmissions, and exhaust systems, which are manufactured by a network of specialized suppliers. In contrast, EVs require components like batteries, electric motors, and power electronics, many of which are produced by a different set of suppliers. This shift is forcing traditional automakers to reevaluate their supply chain strategies, often requiring them to form new partnerships and invest in new technologies.
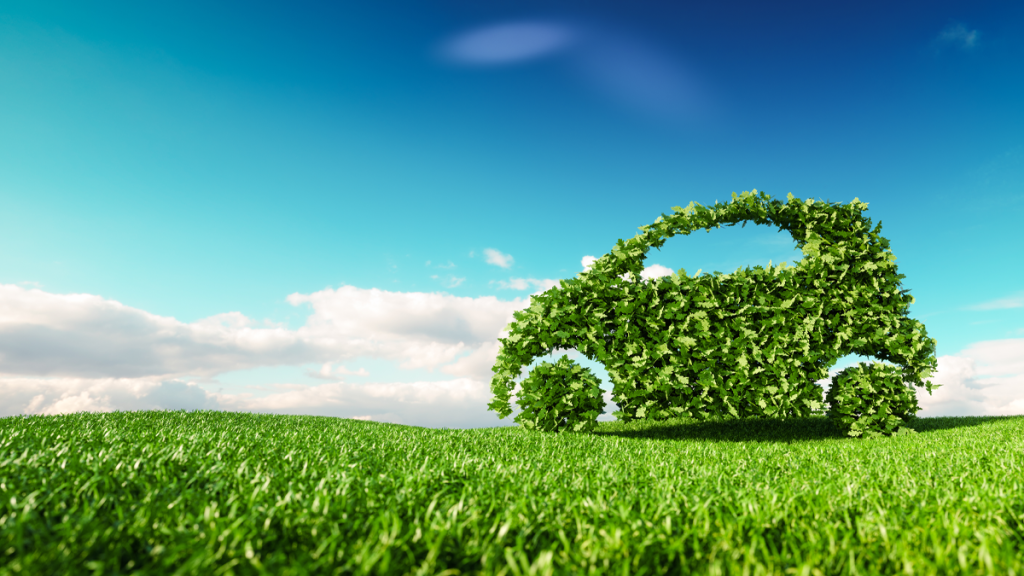
Battery Production: A Critical Challenge
Battery production is one of the most critical aspects of the EV supply chain, and it is also one of the most challenging. The production of lithium-ion batteries requires significant investment in raw materials, manufacturing facilities, and technology. Automakers are increasingly taking control of their battery supply chains by building their own gigafactories or forming joint ventures with battery manufacturers. For example, General Motors has partnered with LG Energy Solution to build Ultium Cells LLC, a joint venture that will produce batteries for GM’s EVs. Similarly, Volkswagen has formed a joint venture with Northvolt to produce batteries for its electric vehicles. These partnerships are helping automakers secure their battery supply and reduce costs, but they also require significant investment and coordination.
Workforce Transformation: Retraining and Upskilling
The shift to electric vehicles is also transforming manufacturing processes and employment in the automotive industry. EV production requires different skills and expertise than ICE production, particularly in areas like battery assembly, software integration, and electric drivetrain manufacturing. This is leading to changes in the workforce, with automakers investing in retraining and upskilling programs to prepare their employees for the demands of EV production.
For example, Ford has launched a $30 million training initiative to prepare its workforce for the transition to electric and autonomous vehicles. Similarly, Volkswagen is partnering with unions and educational institutions to ensure a smooth transition for its employees. These efforts are critical for helping workers adapt to the changing demands of the automotive industry and secure new opportunities in the EV era.
The Competitive Landscape: New Players and New Rules
The EV market is not just a technological shift; it’s also a competitive shift. Traditional automakers are no longer competing solely with each other but also with new players like Tesla, Rivian, and Chinese EV manufacturers. These new entrants bring different strengths to the table, such as expertise in software, battery technology, and user experience, challenging traditional automakers to innovate and adapt.
Tesla, in particular, has set a high bar for the EV market, with its vertically integrated approach, focus on software, and strong brand identity. The company’s success has forced traditional automakers to rethink their strategies and accelerate their electrification plans. For example, Ford has launched the Mustang Mach-E and F-150 Lightning to compete with Tesla’s Model Y and Cybertruck, while General Motors has introduced the Chevrolet Bolt and GMC Hummer EV.
Chinese EV manufacturers, such as BYD, NIO, and XPeng, are also emerging as major players in the global EV market. These companies are leveraging government support, low production costs, and a rapidly growing domestic market to challenge established automakers. For example, BYD has become one of the world’s largest EV manufacturers, with a diverse lineup of electric cars, buses, and trucks. NIO, known for its premium electric SUVs, is expanding into Europe and other markets, posing a significant threat to traditional automakers.
The Future of Traditional Automakers in the EV Era
As the automotive industry continues to transition to electric vehicles, traditional automakers face a critical juncture. Those that can successfully adapt to the new realities of the EV era will be well-positioned to thrive in a low-emission world. However, this will require a proactive approach, with a focus on innovation, collaboration, and workforce development.
At the same time, the rise of electric vehicles is creating opportunities for traditional automakers to redefine their role in the automotive industry. By embracing electrification and sustainability, automakers can enhance their brand reputation, attract new customers, and lead the next generation of mobility solutions. The future of the automotive industry is electric, and traditional automakers have the opportunity to shape this future by leveraging their strengths and embracing the challenges of the transition.