The global shift toward electric vehicles (EVs) is arguably the most significant transformation the automotive industry has experienced in recent decades. As consumers and governments increasingly demand cleaner, more sustainable transportation options, traditional car manufacturers—those long accustomed to internal combustion engine (ICE) vehicles—are facing new challenges. The transition from fossil-fuel-powered vehicles to electric cars is not just a technological overhaul; it is reshaping the entire automotive supply chain, from sourcing raw materials to distribution and final sales.
For established automakers, this transition to electric vehicles presents a complex set of supply chain challenges. How will they manage these challenges while continuing to produce competitive products and maintain profitability? In this article, we explore how traditional manufacturers are responding to the pressures brought on by the electrification wave, focusing on key supply chain challenges such as battery production, raw material sourcing, retooling manufacturing plants, and the integration of new technologies.
The Core Challenges Traditional Manufacturers Face in the EV Supply Chain
1. Sourcing Raw Materials: The Lithium, Cobalt, and Nickel Dilemma
One of the most immediate and pressing challenges in the transition to electric vehicles is securing the raw materials required for batteries. Electric car batteries, particularly lithium-ion batteries, rely heavily on raw materials like lithium, cobalt, nickel, and graphite. As demand for EVs surges, the need for these materials increases exponentially.
For traditional automakers used to sourcing components for internal combustion vehicles, this is a whole new ball game. Here are the primary challenges:
- Securing Long-Term Supply Contracts: Automakers must establish long-term relationships with mining companies to ensure a consistent and affordable supply of essential materials. Companies like Volkswagen, General Motors, and Ford have already started securing long-term agreements with suppliers in countries like Australia, Chile, and the Democratic Republic of Congo. However, securing these contracts often involves navigating political, environmental, and ethical concerns, as some of the materials required for EV batteries are mined in countries with weak labor laws and questionable environmental regulations.
- Supply Chain Bottlenecks: The automotive industry is accustomed to procuring materials like steel, aluminum, and rubber, which are relatively straightforward in terms of availability and supply chains. Lithium, nickel, and cobalt are not as widely available, and their extraction is often tied to complex geopolitical issues. The global demand for these materials is expected to rise significantly, which could create bottlenecks and increase costs—putting pressure on automakers to adapt quickly.
- Ethical Sourcing and Transparency: Ethical sourcing of raw materials, particularly cobalt, is becoming a significant issue due to the exploitative mining practices often found in regions with weak labor protections. Traditional manufacturers are under increasing pressure from both consumers and regulatory bodies to ensure that their supply chains are free from human rights abuses and environmental damage. In response, many are adopting traceability technologies and working with NGOs to ensure a sustainable and ethical supply chain.
2. Battery Production: Scaling Up and Managing Costs
The battery is, by far, the most expensive component of an electric vehicle. For traditional manufacturers that have historically relied on large-scale assembly of engines and drivetrains, EV battery production represents a completely new and complex challenge. Here’s why:
- Gigafactories and Vertical Integration: To reduce costs and ensure a steady supply of batteries, many traditional automakers are building or partnering with gigafactories dedicated to battery production. Tesla has already demonstrated the advantages of vertical integration, where they not only design but also produce their own batteries. In response, traditional carmakers like Volkswagen and BMW are making substantial investments in battery manufacturing through joint ventures with companies like Northvolt and LG Chem. Establishing such factories requires massive capital investment, cutting-edge technology, and expertise in manufacturing—areas where many traditional automakers must play catch-up.
- Reducing Battery Costs: As the demand for EVs grows, automakers must find ways to bring down the high cost of batteries. The price of lithium-ion batteries has been steadily falling, but it still constitutes a significant portion of the vehicle’s overall cost. Manufacturers are exploring ways to develop next-generation batteries, such as solid-state batteries or lithium iron phosphate (LFP) batteries, which may offer higher energy density and lower production costs. However, these technologies are still in the early stages of commercialization, and it may take years before they become viable at scale.
- Battery Recycling and Second-Life Usage: Traditional manufacturers are also looking at ways to address the end-of-life issues associated with EV batteries. As EV adoption accelerates, so will the need to recycle used batteries effectively. Automakers are developing technologies to extract and reuse critical materials like lithium and cobalt from used batteries, which could alleviate some of the pressure on the raw material supply chain. Additionally, used EV batteries could be repurposed for energy storage solutions, contributing to a circular economy within the automotive industry.
3. Retooling Manufacturing Plants and Facilities
Shifting from producing gasoline-powered vehicles to electric vehicles is no simple task—it requires a significant overhaul of manufacturing facilities. Traditional automakers face several hurdles in retooling their factories to accommodate the unique needs of electric vehicle production:
- Production Line Reconfiguration: Traditional ICE vehicles rely on complex systems of engines, transmissions, and exhaust systems. In contrast, EVs have electric motors, inverters, and battery packs as their core components. This means traditional manufacturers must reconfigure their assembly lines to accommodate the production of EVs. For instance, Ford has repurposed its iconic Michigan Assembly Plant to produce the Mustang Mach-E electric SUV. Similarly, General Motors has invested in updating its Detroit-Hamtramck Plant for electric vehicle production.
- Investing in EV-Specific Technologies: The move toward EV manufacturing also means automakers must invest heavily in new technologies like automated battery assembly and advanced robotics. Traditional automakers accustomed to ICE vehicle production may need to acquire specialized expertise and technology partners to develop these capabilities.
- Production Scale and Efficiency: EVs currently make up a smaller proportion of overall vehicle production compared to gasoline cars, but as demand grows, automakers must scale up their production processes while maintaining cost efficiency. While Tesla and BYD have already demonstrated impressive EV production scales, traditional manufacturers are still playing catch-up in terms of achieving cost-effective mass production of electric vehicles.
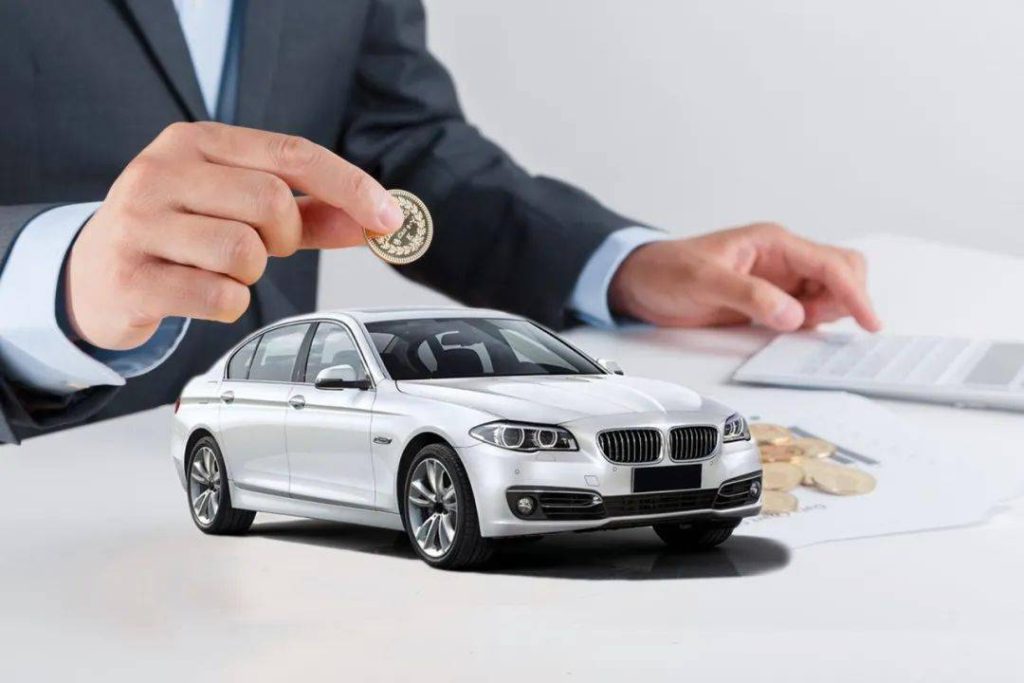
4. The Integration of Advanced Technologies: Autonomous Driving and Connectivity
As the automotive industry transitions to electric vehicles, it’s also embracing new technologies like autonomous driving and connected car systems. Traditional automakers, once focused solely on vehicle design and production, now have to become technology companies in their own right.
- Autonomous Vehicle Development: EVs are often positioned as the platform for autonomous driving technology, as electric powertrains offer advantages in terms of precise control and efficiency. However, developing self-driving cars requires massive investments in artificial intelligence (AI), machine learning, sensors, and real-time data processing. Traditional automakers must forge partnerships with technology companies like Google’s Waymo, Aurora, and Mobileye to compete in the rapidly growing field of autonomous vehicles.
- Connectivity and Over-the-Air (OTA) Updates: The expectation for in-car connectivity has never been higher, with consumers demanding features like seamless infotainment systems, real-time traffic data, and OTA updates. Companies like Tesla have pioneered this connected experience, offering customers the ability to receive updates remotely without visiting the service center. To compete, traditional automakers need to integrate cutting-edge software development capabilities, which may require hiring new talent or collaborating with software companies.
5. Managing the Talent Shift
The shift to electric mobility also requires a shift in talent. Traditional automakers must attract and retain engineers and developers with expertise in electric powertrains, battery technology, software development, and autonomous systems.
- Skilling and Reskilling: Traditional automakers may need to invest in training programs to ensure their workforce is prepared for the electrified future. This includes reskilling existing employees to handle the new demands of EV production, as well as hiring fresh talent from fields like robotics, AI, and battery engineering.
- Partnerships with Tech Firms: Many automakers are increasingly partnering with technology firms to tap into the expertise needed for this transition. For instance, BMW has teamed up with Intel and Mobileye to work on autonomous driving technologies, while Ford has formed partnerships with companies like Google to enhance its software and data capabilities.
Conclusion: Navigating the Road Ahead
The electrification of the automotive industry is a monumental shift that will require traditional manufacturers to make dramatic changes across their entire supply chain. From securing raw materials and ramping up battery production to retooling factories and embracing new technologies, the transition to EVs is not without its challenges. However, traditional manufacturers are not sitting idly by. They are responding to the pressures with strategic investments, partnerships, and innovations aimed at building a future-proof supply chain that can support the growing demand for electric mobility.
While the journey is fraught with difficulties, the rewards for successfully navigating these challenges are significant. The future of the automotive industry will be defined by those companies that can adapt quickly, innovate boldly, and embrace the opportunities that come with the rise of electric vehicles. The road to electrification may be long and winding, but for those who can meet the challenges head-on, it offers an exciting future of growth, sustainability, and innovation.