The rise of electric vehicles (EVs) is transforming not only the automotive market but also the very production models that have underpinned the traditional automotive industry for over a century. From assembly lines to supply chains, manufacturing technologies, and workforce dynamics, the shift from internal combustion engine (ICE) vehicles to electric vehicles (EVs) is shaking the core of how established carmakers design, build, and deliver their products.
For traditional automakers, the transition to electric mobility is not just about producing a different kind of vehicle—it’s about fundamentally overhauling their entire production system. The production model that served these companies well for decades, based on efficient assembly lines designed for ICE vehicles, is now being called into question. The disruptive changes are forcing traditional manufacturers to rethink their approach to manufacturing processes, product design, technology integration, and supply chain management.
1. Streamlining Production Lines: From Engines to Electric Drivetrains
One of the most immediate and visible impacts of the shift to electric vehicles is the reconfiguration of production lines. In the traditional ICE vehicle, the engine is the heart of the car, with a complex array of internal combustion engines, transmissions, and exhaust systems being assembled. However, in an electric vehicle, the electric motor and battery pack are the key components, which fundamentally alters the production process.
Simplification of Components
- Fewer moving parts: Traditional ICE vehicles have many more moving parts—an engine, a transmission system, a cooling system, an exhaust system, and so on. In contrast, electric vehicles have a simpler powertrain consisting of the electric motor, battery pack, and electronic controls. This simplification reduces the number of components required and changes the way parts are assembled.
- Impact on assembly lines: With fewer parts to assemble, traditional automakers face the challenge of retooling and retraining their workforce to handle electric drivetrains and batteries. Assembly lines that were once dedicated to assembling complex engines and transmissions now need to accommodate the assembly of battery packs and electric motors, which require different processes, equipment, and materials. This means that factory layouts and production workflows must be completely revamped.
- New assembly methods: The production of electric drivetrains requires specialized equipment for handling battery cells, thermal management, and electrical systems. Companies like Tesla have already streamlined the production of electric drivetrains with automation and highly efficient assembly lines. Traditional automakers are now looking to incorporate similar strategies, such as robotic assembly and AI-powered quality control systems, to make EV production more cost-effective.
2. Scaling Up Battery Production and Securing the Supply Chain
A critical shift in production models for traditional manufacturers is the need to scale up battery production. Unlike ICE vehicles, which use a well-established supply chain of engines, fuel systems, and exhaust components, EVs rely on batteries, which are not only complex to produce but also expensive.
Challenges of Battery Sourcing
- Battery procurement: Automakers are now required to secure large quantities of high-quality batteries. This has led to a global scramble for battery suppliers and strategic partnerships with battery manufacturers like LG Chem, Panasonic, and CATL. Companies such as General Motors and Ford have even invested in building their own battery factories in collaboration with suppliers, like Ultium Cells (GM and LG Chem’s joint venture) to gain better control over production costs and supply chain stability.
- Localized battery production: The cost of batteries represents one of the largest expenses for EVs, and traditional manufacturers need to figure out ways to bring the production cost down. Some companies are exploring vertical integration by controlling their own battery manufacturing processes, while others are looking to localize battery production to reduce costs and increase efficiency in their supply chains. For example, Volkswagen has invested in battery production facilities in Europe to meet growing demand.
Battery Recycling and Sustainability
- Recycling technology: Traditional automakers are also investing in battery recycling technologies to reduce dependence on raw materials and to make their production models more sustainable. Recycling used EV batteries can help recover critical materials like lithium, nickel, and cobalt, ensuring a more sustainable supply chain. Companies like BMW and Ford are experimenting with second-life battery usage and exploring battery recycling solutions to minimize waste and environmental impact.
- Strategic sourcing of raw materials: In addition to securing battery production, automakers are also working on securing long-term supply agreements for the raw materials required in battery production, such as lithium, cobalt, and nickel. With the growing demand for these materials, some traditional manufacturers are establishing partnerships with mining companies or investing in the extraction and refinement of these critical materials.
3. The Shift to Flexible and Agile Manufacturing Systems
As the automotive industry embraces electrification, the focus is shifting from the mass production of standardized ICE vehicles to more flexible manufacturing systems capable of producing a wide variety of EV models—ranging from economical electric cars to luxury electric sedans and performance electric vehicles.
Modular Production Systems
- Platform strategy: Traditional manufacturers are adopting a platform-based production model, where a single vehicle platform can be used for multiple types of electric vehicles. For instance, Volkswagen Group has introduced the MEB (Modular Electric Drive Matrix) platform, which can be used for a variety of EVs across their brands, from the Volkswagen ID.3 to the Audi e-tron. This reduces production complexity and allows automakers to scale up production quickly and efficiently.
- Agile production: With the need to adapt to consumer demand for different types of EVs, traditional manufacturers must move away from rigid, assembly-line production models toward more flexible and agile production systems. This includes the ability to customize production schedules, adjust vehicle features on the fly, and introduce new models into production without extensive retooling.
Decentralized Manufacturing and Gigafactories
- Gigafactories: Many established automakers are following Tesla’s lead in building gigafactories dedicated to producing large volumes of electric vehicles and batteries. This approach requires massive capital investment, sophisticated manufacturing systems, and highly efficient supply chain management. Traditional manufacturers like BMW, Ford, and General Motors are actively working to build or partner with gigafactories to increase their EV production capacity.
- Supply chain diversification: To maintain flexibility and control over the production process, traditional manufacturers are diversifying their supply chains to ensure resilience. With the global chip shortage and supply chain disruptions in recent years, automakers are looking to mitigate risks by moving towards more regionalized supply chains and investing in local production capabilities for EV components, particularly batteries.
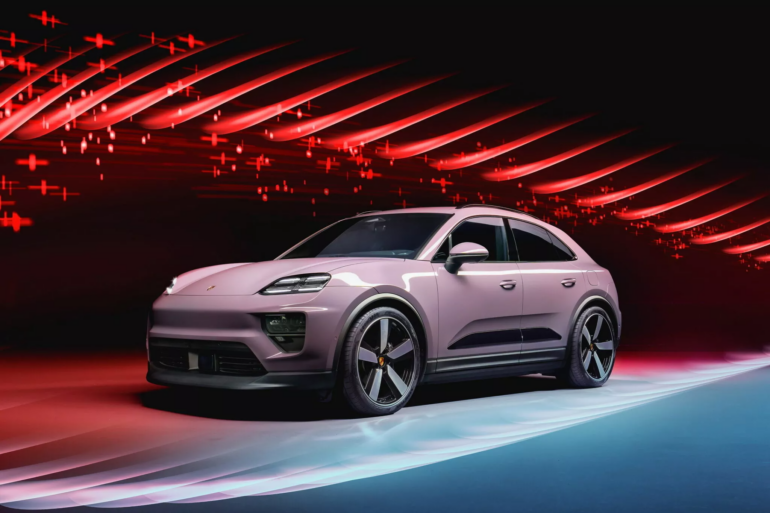
4. The Technological Shift: Digitalization and Automation
The integration of digital technologies into the production process is another key area where traditional automakers are facing disruption. Electric vehicles are not just about different powertrains; they also feature advanced technologies like autonomous driving, connected car systems, and over-the-air (OTA) updates. These technologies are requiring traditional manufacturers to update their production methods and factory automation systems.
Smart Manufacturing and Industry 4.0
- Automation: As electric vehicles have fewer moving parts compared to ICE vehicles, the assembly process requires different automation technologies. Traditional automakers are adopting advanced robotic systems and AI-driven quality control to ensure high precision and efficiency in the assembly of EVs. Automated guided vehicles (AGVs) and 3D printing technologies are also being integrated into production lines to reduce labor costs and enhance flexibility.
- Digitalization: Traditional manufacturers are increasingly incorporating digital twin technology, machine learning, and AI into their production processes to monitor, optimize, and automate various aspects of manufacturing. These technologies can significantly reduce errors, improve quality control, and lower production costs. As a result, traditional automakers are embracing smart factories that collect data in real time to drive operational decisions.
Software Integration
- Over-the-air updates: As EVs become more software-centric, traditional manufacturers must invest in software development and digital infrastructure to enable OTA software updates. Unlike traditional vehicles, EVs can improve over time through remote software updates, meaning that automakers now need to develop robust systems to push updates to customers and ensure the continuous improvement of the vehicle’s functionality.
- Autonomous driving technology: Another key technology that disrupts traditional production models is the integration of autonomous driving systems into EVs. Traditional automakers must now collaborate with tech firms and invest in the development of AI systems, sensors, and data processing capabilities for self-driving cars. These new capabilities introduce entirely new supply chain requirements and necessitate specialized components, such as LiDAR, radar sensors, and camera systems.
5. Workforce and Talent Shift
As the production model evolves, so too must the workforce. Traditional automakers are facing a significant skills gap as they transition to electric vehicle production. Workers must be retrained to handle new technologies, such as electric drivetrains, battery assembly, and advanced automation systems.
Reskilling and Upskilling
- Training programs: To bridge the gap, traditional manufacturers must implement reskilling and upskilling programs to ensure their workforce is prepared for the changes. Training on EV manufacturing processes, software engineering, and robotics is crucial to maintain efficiency and quality as production models evolve.
- Collaboration with tech companies: Many traditional manufacturers are partnering with technology companies to bring in specialized knowledge in areas like software development, autonomous systems, and digital manufacturing. This creates a hybrid workforce combining traditional engineering expertise with cutting-edge technological skills.
Conclusion: Navigating the Disruption
The rise of electric vehicles represents a paradigm shift in how cars are made, with significant implications for traditional automakers’ production models. As the industry embraces new technologies, more flexible production systems, and sustainable supply chains, the future of car manufacturing will look very different from the past.
While the transition to EVs presents challenges, it also offers an opportunity for traditional automakers to reimagine their production systems. By adopting advanced technologies, investing in new capabilities, and rethinking their supply chains, traditional manufacturers can not only stay competitive in the electric vehicle era but also shape the future of the automotive industry.