Introduction: The Era of Electric Vehicles and Its Impact on Traditional Automakers
The automotive industry is undergoing a profound transformation, driven by the rise of electric vehicles (EVs). With growing concerns over climate change, rising fuel prices, and increased government pressure to reduce carbon emissions, electric mobility has gained significant traction in recent years. As a result, traditional automotive manufacturers, who have long been reliant on internal combustion engine (ICE) vehicles, are facing new technological innovations, production challenges, and an evolving competitive landscape.
Electric vehicles represent a significant departure from conventional cars in several key areas, including powertrains, battery technology, energy efficiency, and manufacturing processes. For traditional automakers, the shift to EV production is not just a response to market demand—it is an imperative to stay competitive in a rapidly changing industry. This article explores how traditional automotive manufacturers are adapting to the technological innovations introduced by electric vehicles, and the production challenges they face in integrating these technologies into their existing operations.
Section 1: The Technological Challenges of Electric Vehicle Production
1.1 Transitioning from Internal Combustion Engines (ICE) to Electric Powertrains
One of the most significant technological challenges traditional automakers face is the transition from internal combustion engine (ICE) vehicles to electric powertrains. This shift requires automakers to retool their entire manufacturing processes, as electric vehicles are fundamentally different from gasoline-powered cars in terms of design, components, and assembly.
- Powertrain Redesign: The electric powertrain, which consists of an electric motor, battery pack, inverter, and other electronics, is vastly different from the internal combustion engine and its associated parts (e.g., pistons, crankshafts, fuel injectors). Traditional carmakers must design and integrate new battery management systems (BMS), electric motors, and charging systems into their production lines.
- Fewer Components, but More Complexity: While electric vehicles typically have fewer mechanical components than ICE vehicles, the electronic and software components of EVs present new challenges. These include power electronics, thermal management systems, and advanced sensors. The increased reliance on electronics means that automakers must collaborate closely with tech companies and invest in software development and data management to ensure vehicle performance and safety.
1.2 Battery Technology: The Heart of Electric Vehicle Innovation
The battery is perhaps the most critical component of an electric vehicle, and it represents one of the most significant technological challenges for traditional automakers. Batteries for electric vehicles are large, complex, and expensive, and they require sophisticated supply chains to source materials and manage production.
- Battery Supply Chain: The production of lithium-ion batteries, which power most electric vehicles, relies on materials like lithium, cobalt, nickel, and graphite. Automakers must secure stable supply chains for these materials, which are often sourced from specific regions of the world. Geopolitical instability or fluctuating raw material prices can pose a risk to automakers’ ability to produce EVs at scale.
- Battery Efficiency and Cost Reduction: One of the biggest challenges in battery technology is improving energy density—how much energy a battery can store relative to its size and weight. Traditional automakers are investing heavily in solid-state batteries and other next-generation technologies that promise to deliver longer range, faster charging, and lower costs. However, mass production of these advanced batteries remains a significant hurdle.
1.3 Advancing Charging Infrastructure and Range Capabilities
To make electric vehicles viable alternatives to traditional vehicles, automakers must also consider charging infrastructure and range capabilities. While the range of EVs has improved significantly, many consumers remain concerned about the availability of charging stations and the time required to recharge a vehicle.
- Range Anxiety: Traditional automakers must address range anxiety, the fear that an electric vehicle will run out of battery before reaching a charging station. By investing in larger battery packs and more efficient powertrains, automakers are gradually increasing the driving range of electric vehicles. However, the battery’s size and weight impact vehicle performance and energy consumption, so automakers must balance range improvements with efficiency and cost.
- Charging Networks: Another challenge is the expansion of public charging infrastructure. Automakers must collaborate with governments, private companies, and utilities to expand fast-charging networks. Companies like Tesla have set the example with their proprietary charging stations, while others are developing universal networks to make long-distance EV travel more feasible.
Section 2: Production Challenges and Strategies for Transition
2.1 Reworking Manufacturing Facilities
The shift to electric vehicle production requires automakers to transform their manufacturing facilities, which were previously designed for the assembly of internal combustion engine vehicles. This transformation involves significant investments in new equipment, training, and production line adjustments.
- Re-tooling Factories: Automakers must invest in retooling existing factories to accommodate the production of electric vehicles. This may involve upgrading equipment to handle the assembly of electric powertrains, installing new systems for battery integration, and ensuring that facilities are capable of mass-producing complex electronic components.
- Automation and Robotics: Given the complexity of electric vehicle production, many automakers are turning to automation and robotics to improve efficiency, reduce labor costs, and ensure high levels of precision in the manufacturing process. For example, robots are essential for battery assembly, powertrain installation, and quality control.
2.2 Sourcing Raw Materials and Managing Costs
One of the most critical challenges for traditional automakers in the transition to electric vehicle production is sourcing the raw materials required for batteries and other components. Lithium, cobalt, and nickel are essential for the production of lithium-ion batteries, but they are often concentrated in specific regions of the world, creating supply chain risks.
- Diversifying Sourcing: To mitigate the risks associated with raw material supply, automakers are exploring ways to diversify their sources of key materials. Some automakers are forming strategic partnerships with mining companies to secure long-term access to essential minerals. Others are investing in the development of recycling technologies to reuse materials from old batteries and reduce reliance on new mining operations.
- Cost Reduction: Battery costs are a significant portion of an electric vehicle’s overall price. As demand for electric vehicles increases, automakers are under pressure to reduce these costs. This has led to a focus on economies of scale, battery chemistry improvements, and better manufacturing processes to lower the price of EV batteries and make them more affordable for consumers.
2.3 Addressing Workforce Challenges
The shift from producing internal combustion engine vehicles to electric vehicles also requires automakers to address significant workforce challenges. Electric vehicles involve more sophisticated technology, and traditional workers may need to be retrained to handle new systems, such as electric drivetrains, battery assembly, and advanced electronics.
- Training and Reskilling: As automakers transition to electric vehicle production, they must invest in training and reskilling programs to ensure that their workforce has the skills required to handle the new technologies. This includes providing training in areas such as robotics, battery management systems, electric powertrains, and autonomous vehicle technologies.
- Labor Relations: The transition to EV production may also have an impact on traditional automotive labor unions, which have historically represented workers in ICE vehicle production plants. As new technologies are introduced, unions must adapt to new labor dynamics and work with automakers to ensure a smooth transition for workers.
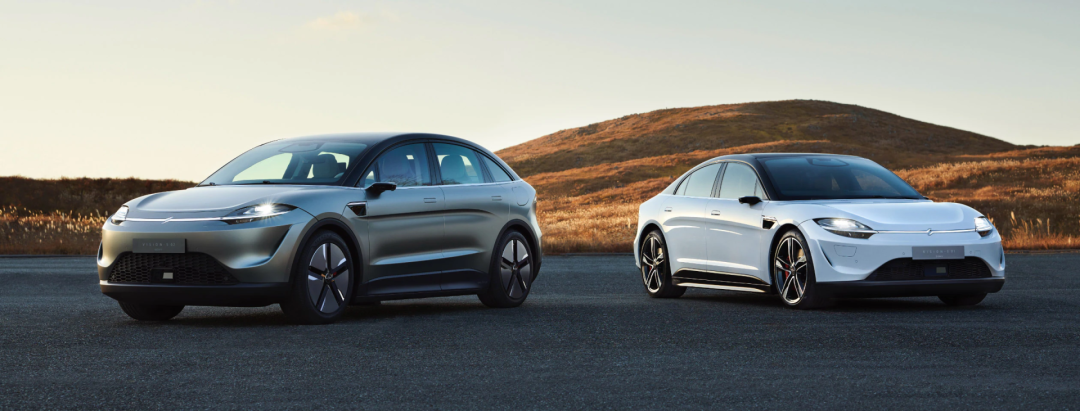
Section 3: The Strategic Response of Traditional Automakers
3.1 Developing New Electric Models
To compete in the EV market, traditional automakers are developing new electric vehicle models that appeal to a broader range of consumers. Many automakers are launching fully electric models alongside their traditional ICE offerings, covering a wide spectrum of vehicle types, from electric sedans and SUVs to electric trucks.
- Branding and Market Positioning: Some automakers, such as Ford, Volkswagen, and General Motors, are positioning themselves as key players in the electric vehicle market. These companies are investing heavily in electric mobility to enhance their brand image and respond to growing consumer demand for sustainable transportation options.
- Innovation in Design: Traditional automakers are also leveraging the unique design opportunities presented by electric powertrains. Without the constraints of a bulky internal combustion engine, automakers have greater flexibility in terms of vehicle layout, interior space, and aerodynamics. This has led to the development of more stylish and innovative EV designs that cater to evolving consumer preferences.
3.2 Collaborations and Partnerships
Recognizing the complexities of transitioning to electric vehicle production, many traditional automakers are forming strategic collaborations and partnerships with technology companies, suppliers, and startups specializing in EV technologies.
- Joint Ventures: Several automakers have entered into joint ventures with battery manufacturers, such as LG Chem, Samsung SDI, and Panasonic, to secure a stable supply of batteries for their EVs. These partnerships allow automakers to leverage the expertise of battery producers while securing long-term supply contracts for essential components.
- Collaborations with Tech Firms: As electric vehicles become more technologically advanced, automakers are also partnering with tech companies to incorporate cutting-edge features such as autonomous driving, infotainment systems, and connectivity into their electric vehicles. Companies like Google, Apple, and Nvidia are playing key roles in this aspect of EV development.
Conclusion: A Challenging Yet Opportunity-Rich Transition
The transition from traditional internal combustion engine vehicles to electric vehicles is a monumental challenge for traditional automakers. It requires significant technological innovation, production adjustments, and strategic repositioning. However, it also presents a tremendous opportunity for automakers to reshape their business models, diversify their product offerings, and lead the way in the rapidly growing electric vehicle market.
To succeed, traditional automakers must embrace technological advancements, streamline production processes, and collaborate with key players in the battery and charging infrastructure sectors. With the right strategies in place, the shift to electric vehicles can become a competitive advantage, positioning traditional automakers as leaders in the sustainable mobility revolution.