The global automotive industry is undergoing a profound transformation, driven by the increasing adoption of electric vehicles (EVs). This shift presents significant opportunities and challenges, not only for automakers but also for the broader automotive supply chain. Traditional automotive suppliers—those that have built their businesses around the production of components for internal combustion engine (ICE) vehicles—are now facing a new reality. The transition to electric vehicles is reshaping the industry, and suppliers must adapt or risk becoming obsolete.
This article investigates how the shift to electric vehicles is affecting traditional automotive suppliers and their supply chain operations. We will assess the impact on various sectors within the supply chain, explore the strategic responses from suppliers, and discuss the broader implications for the automotive industry. Additionally, we will look at the competitive dynamics in the industry as suppliers navigate this seismic shift.
The Shift to Electric Vehicles: A Game Changer for the Automotive Industry
Electric vehicles, once considered a niche market, have moved into the mainstream. Governments around the world have introduced stricter emissions regulations, while consumer preferences are shifting toward more sustainable, environmentally friendly transportation options. The global automotive market is projected to continue its transition towards electric vehicles, with automakers increasingly investing in EV production.
This transition is transforming the traditional automotive supply chain. In an ICE vehicle, key components such as the engine, exhaust system, fuel tank, and transmission make up a significant portion of the supply chain. In contrast, an electric vehicle relies heavily on components like the battery, electric motor, power electronics, and charging systems, which fundamentally alters the landscape of automotive supply chains.
Traditional Automotive Suppliers: The Core of the Supply Chain
The traditional automotive supply chain consists of several layers of suppliers, ranging from Tier 1 suppliers (those providing components directly to manufacturers) to Tier 2 and Tier 3 suppliers (those providing subcomponents and raw materials to higher-tier suppliers). For decades, these suppliers have been focused on providing parts and systems for internal combustion engine vehicles.
For instance, companies that supply engine components, fuel systems, exhaust systems, and transmissions have historically been key players in the automotive supply chain. As the industry pivots to electric vehicles, these suppliers are facing significant challenges. In many cases, the parts they produce for ICE vehicles are no longer needed in electric vehicles, forcing them to reassess their business models and strategies.
The Impact of Electric Vehicles on Traditional Automotive Suppliers
As the demand for electric vehicles grows, traditional suppliers are experiencing several key impacts, which can be categorized into technological, operational, and strategic challenges.
1. Shift in Demand for Traditional Components
Electric vehicles (EVs) require fewer parts than internal combustion engine (ICE) vehicles. EVs lack components like the internal combustion engine, transmission, fuel system, and exhaust system. This shift means that suppliers focused on these components are seeing a dramatic decline in demand for their products. For example, companies that produce engine parts, exhaust systems, and fuel pumps face uncertainty about their future as the demand for these parts dwindles.
On the other hand, the demand for new components associated with electric vehicles is increasing. Batteries, electric motors, power electronics, and charging systems are now essential parts of the supply chain. Suppliers that have traditionally focused on ICE vehicle components are finding themselves needing to either pivot or form partnerships with new companies to access these emerging opportunities.
2. Increased Demand for Batteries and Battery Components
The battery is the heart of any electric vehicle. As a result, suppliers who can provide high-quality batteries or critical battery components are positioned to benefit from the shift to EVs. However, the battery supply chain is complex and capital-intensive. Lithium-ion batteries, which are most commonly used in EVs, require raw materials such as lithium, cobalt, nickel, and graphite. These materials are often sourced from global markets, and the supply of these materials is subject to fluctuations in price and availability.
Traditional suppliers who have not been involved in battery production must now either invest in new technologies or partner with battery manufacturers to stay competitive. Companies such as Panasonic, LG Chem, and CATL are at the forefront of EV battery production, but traditional suppliers like Bosch, Continental, and Magna are also looking to enter this space. The growth in battery demand is also encouraging established automotive suppliers to vertically integrate their operations to gain more control over battery production and raw material procurement.
3. Electrification of Powertrains
While electric vehicles do not have traditional engines or transmissions, they still rely on complex powertrains that require a variety of components. These include electric motors, inverters, power control units, and regenerative braking systems. Traditional automotive suppliers must now pivot their focus to designing and manufacturing these new electric powertrain components.
Some established suppliers are already making strides in this area. For example, Bosch, a supplier traditionally focused on ICE systems, has developed electric motor technologies for use in EVs. Similarly, ZF Friedrichshafen, known for its work on transmissions and drivetrains, has begun developing electric drivetrains for electric vehicles. However, entering this market requires significant R&D investments and expertise in electric vehicle technologies, which can be a challenge for suppliers accustomed to working with ICE components.
4. Supply Chain Restructuring and New Partnerships
The shift to electric vehicles is forcing traditional suppliers to restructure their supply chains. Many suppliers are reevaluating their supplier relationships, seeking new partnerships, and in some cases, forming joint ventures to develop new technologies. For instance, automotive suppliers like Magna and Bosch are increasingly collaborating with EV startups and automakers to co-develop electric vehicle components.
In addition to new partnerships within the automotive industry, traditional suppliers are also looking for opportunities to collaborate with tech companies. The software and digital systems that power EVs are crucial for their operation, and many automotive suppliers are now working with companies specializing in artificial intelligence, data analytics, and autonomous driving technologies to ensure their components meet the evolving demands of the EV market.
5. Impact on Aftermarket Suppliers
The aftermarket segment of the automotive supply chain, which focuses on replacement parts and services, is also being affected by the rise of electric vehicles. EVs typically have fewer moving parts and require less maintenance than ICE vehicles. As a result, traditional aftermarket suppliers who rely on replacement parts for engines, exhaust systems, and other mechanical components face a reduction in demand for their products.
At the same time, new opportunities are emerging for aftermarket suppliers in the EV space. As more electric vehicles hit the road, there will be growing demand for components related to EV maintenance, including battery management systems, charging equipment, and software updates. Aftermarket suppliers must adapt to this shift by investing in the skills and technologies needed to service the new generation of electric vehicles.
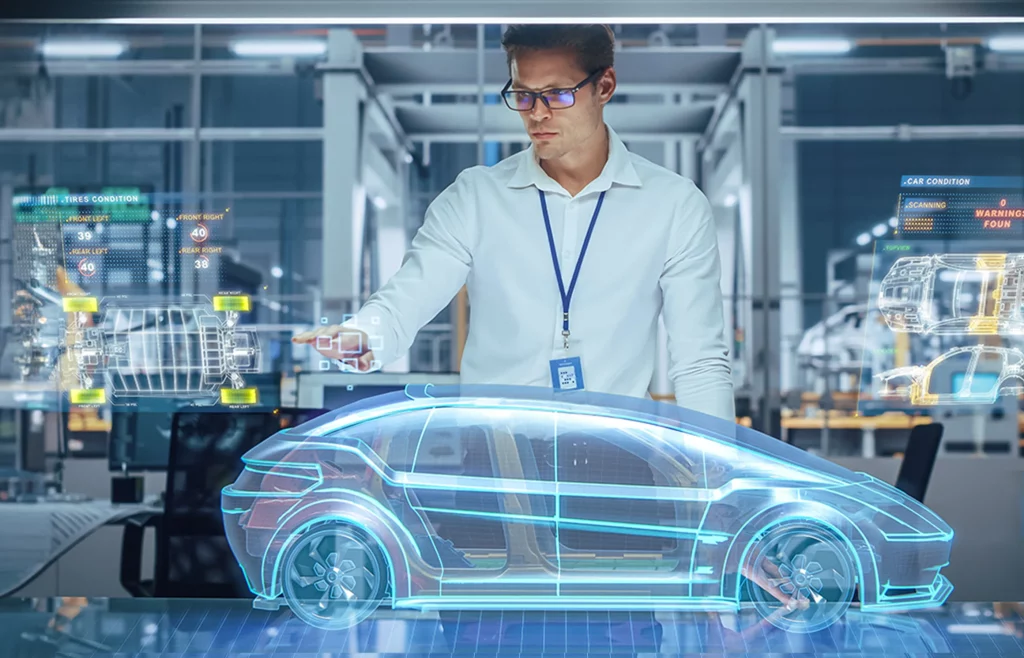
The Strategic Responses of Traditional Suppliers
To navigate the changes brought about by electric vehicles, traditional automotive suppliers are adopting several strategic approaches.
1. Diversification and Innovation
Many traditional suppliers are diversifying their product offerings to include components specific to electric vehicles. For example, Tier 1 suppliers like Bosch and Continental are investing heavily in electric powertrains, battery management systems, and advanced driver-assistance systems (ADAS). These companies are also expanding their R&D efforts to develop new technologies for electric and autonomous vehicles.
Additionally, some suppliers are branching out into new markets beyond traditional automotive components. For example, Bosch is also investing in energy storage solutions and renewable energy technologies, recognizing the growing intersection between the automotive and energy sectors. This diversification helps to mitigate risks and ensures that suppliers are positioned to thrive in the future.
2. Partnerships and Joint Ventures
To mitigate the risks associated with the shift to electric vehicles, traditional suppliers are forming strategic partnerships and joint ventures with automakers, battery manufacturers, and tech companies. These collaborations allow suppliers to share the costs of developing new technologies and gain access to new markets.
For instance, Magna has partnered with LG Electronics to develop electric powertrains for electric vehicles. Similarly, Bosch has joined forces with other companies to develop electric motors, powertrains, and EV charging solutions. These partnerships enable suppliers to remain competitive in the rapidly changing automotive landscape.
3. Vertical Integration
Some traditional suppliers are pursuing vertical integration to gain more control over the electric vehicle supply chain. By taking on more of the production process internally, suppliers can reduce reliance on external partners, secure critical materials, and protect their margins. For example, several suppliers are investing in their own battery manufacturing capabilities or entering the business of recycling EV batteries to recover valuable raw materials.
Vertical integration helps suppliers secure a steady supply of critical components, reducing exposure to fluctuations in raw material prices and ensuring that they can meet the growing demand for electric vehicle parts.
The Competitive Dynamics in the Electric Vehicle Supply Chain
The shift to electric vehicles is fundamentally changing the competitive dynamics of the automotive supply chain. Traditional suppliers that have relied on ICE vehicle components are now competing with a new breed of suppliers that specialize in electric vehicle technologies. Startups focused on electric drivetrains, batteries, and autonomous systems are emerging as formidable competitors, often leveraging their agility and innovative approaches to gain market share.
In addition, tech companies are increasingly entering the automotive supply chain, particularly in areas related to connectivity, autonomous driving, and software. Companies like Google, Apple, and NVIDIA are well-positioned to impact the EV space, given their expertise in AI, data analytics, and consumer electronics.
Traditional automotive suppliers must therefore adapt by investing in innovation, forming strategic partnerships, and embracing new technologies to remain competitive.
Conclusion
The shift to electric vehicles is reshaping the automotive supply chain in profound ways. Traditional suppliers face significant challenges as they transition from ICE vehicle components to electric vehicle technologies. However, by diversifying their portfolios, forming strategic partnerships, and embracing innovation, suppliers can remain competitive and capitalize on the growth of the EV market.
As the automotive industry continues to evolve, suppliers must stay agile and responsive to the changing needs of automakers and consumers. The rise of electric vehicles presents both risks and opportunities, and those suppliers that are able to adapt to the new reality will be best positioned to thrive in the future.