Introduction
The rapid adoption of electric vehicles (EVs) is hailed as a cornerstone of the global transition to sustainable transportation. However, the environmental benefits of EVs are under scrutiny due to challenges associated with lithium-ion battery production, disposal, and resource extraction. While EVs eliminate tailpipe emissions, their reliance on finite minerals (e.g., lithium, cobalt, nickel) and the risks of improper battery disposal pose significant ecological threats. Battery recycling technologies are emerging as a potential solution to mitigate these concerns. This article explores how advancements in recycling methods, policy frameworks, and circular economy models could address the environmental paradox of EVs.
1. The Environmental Dilemma of EV Batteries
1.1 Resource Extraction and Carbon Footprint
EV batteries require large quantities of critical minerals, often mined under environmentally destructive conditions. For example, lithium extraction consumes vast amounts of water and damages ecosystems in regions like South America’s “Lithium Triangle” . Similarly, cobalt mining in the Democratic Republic of Congo has raised ethical and environmental red flags.
1.2 End-of-Life Challenges
By 2030, over 12 million tons of lithium-ion batteries are projected to reach end-of-life globally. If improperly managed, these batteries release toxic heavy metals (e.g., lead, cadmium) and flammable electrolytes, contaminating soil and water . Incineration or landfilling exacerbates air pollution and squanders valuable resources.
2. Current State of Battery Recycling Technologies
2.1 Pyrometallurgy and Hydrometallurgy
Traditional methods like pyrometallurgy (high-temperature smelting) recover metals such as cobalt and nickel but generate harmful emissions and waste slag. Hydrometallurgy, which uses chemical leaching, offers higher purity metal recovery but involves toxic solvents and high energy costs .
2.2 Direct Recycling and Emerging Innovations
Direct recycling preserves battery cathode materials intact, reducing energy use and waste. Startups like Redwood Materials and Li-Cycle are commercializing these methods. Meanwhile, biohydrometallurgy—using microorganisms to extract metals—shows promise for low-carbon, cost-effective recycling .
2.3 Second-Life Applications
“Second-life” repurposing extends battery utility beyond EVs. For instance, retired EV batteries can store renewable energy for grids or power telecom stations. BMW and Nissan have piloted such projects, demonstrating a 30–70% reduction in carbon footprint compared to new battery production .
3. Barriers to Effective Recycling
3.1 Technical Limitations
- Heterogeneity of Batteries: Variations in chemistry (e.g., NMC, LFP) complicate automated disassembly and material recovery .
- Low Recovery Rates: Current methods recover only 50–70% of lithium, with even lower rates for rare earth metals .
3.2 Economic and Regulatory Gaps
- High Costs: Recycling processes remain 2–3 times more expensive than virgin mineral extraction, deterring investment .
- Informal Recycling Networks: Approximately 50% of retired batteries are processed by unregulated entities, risking environmental contamination .
- Policy Fragmentation: Inconsistent regulations across regions hinder standardized recycling practices.
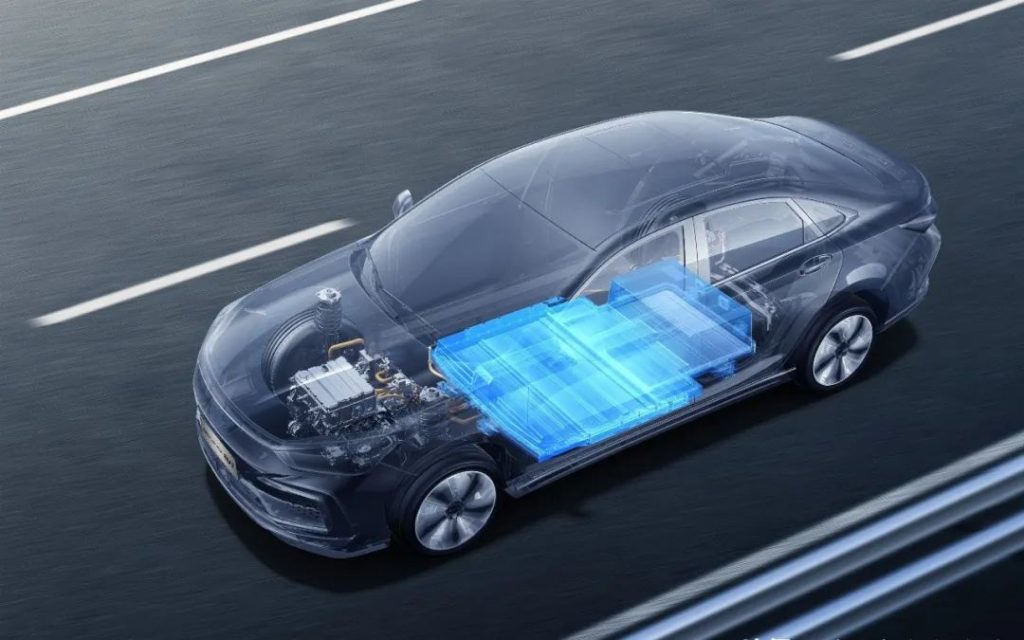
4. Policy and Industry Initiatives Driving Progress
4.1 Legislative Frameworks
The EU’s Battery Regulation mandates minimum recycling efficiencies (e.g., 70% for lithium by 2030) and holds manufacturers financially responsible for collection and recycling. China’s “white list” system accredits compliant recyclers, reducing informal sector dominance .
4.2 Corporate Commitments
Tesla’s Nevada Gigafactory integrates a closed-loop recycling system, aiming to recover 92% of battery materials. Similarly, CATL and BYD are investing in “black mass” processing to extract lithium and cobalt at scale .
4.3 Circular Economy Models
Partnerships between automakers, recyclers, and energy firms are fostering resource loops. For example, Redwood Materials collaborates with Ford and Volvo to create a North American supply chain for recycled battery materials .
5. Case Studies: Successes and Lessons Learned
5.1 Tesla’s Closed-Loop System
Tesla’s in-house recycling facility recovers over 1,300 tons of nickel, 400 tons of copper, and 80 tons of cobalt annually, slashing reliance on newly mined minerals .
5.2 China’s Battery Recycling Networks
China has established over 10,000 collection points, achieving a 40% recycling rate for retired EV batteries. Government subsidies and tech-driven platforms (e.g., CATL’s blockchain traceability system) enhance transparency .
5.3 European Union’s Green Deal
The EU’s €3 billion investment in battery recycling R&D aims to achieve 95% material recovery by 2035, coupled with strict penalties for non-compliant manufacturers .
6. Future Pathways and Innovations
6.1 AI and Automation
Machine learning algorithms can optimize battery disassembly and sorting, while robotics improve precision and safety in handling toxic components .
6.2 Sustainable Material Design
Research into solid-state batteries and cobalt-free cathodes (e.g., lithium iron phosphate) could simplify recycling and reduce dependency on scarce minerals .
6.3 Global Collaboration
International standards for battery labeling, collection, and recycling protocols are critical. Initiatives like the Global Battery Alliance aim to unify efforts across 70+ member organizations .
7. Conclusion: A Balanced Perspective
Battery recycling technologies are indispensable for mitigating the environmental risks of EVs, but they are not a panacea. While advancements in hydrometallurgy, second-life applications, and policy frameworks show significant promise, challenges like economic viability, technical complexity, and regulatory enforcement persist. A holistic approach—combining recycling innovation, ethical mineral sourcing, and consumer education—is essential to fully realize the eco-potential of electric mobility.
The path forward demands collaboration among governments, industries, and researchers to transform EV batteries from an environmental liability into a pillar of the circular economy.