Electric vehicles (EVs) are often hailed as a cleaner, greener alternative to traditional internal combustion engine (ICE) vehicles. However, critics argue that the environmental impact of battery production, particularly lithium mining and manufacturing, undermines the sustainability of EVs. Are these concerns valid, or are they based on misconceptions? This article examines the environmental challenges of lithium mining and battery manufacturing, highlights advancements in sustainable battery production and recycling, and compares the carbon footprint of EVs versus ICE vehicles over their lifespan.
The Environmental Challenges of Lithium Mining and Battery Manufacturing
The production of lithium-ion batteries, which power most electric vehicles, involves complex processes that can have significant environmental and social impacts. Below, we explore the key challenges associated with lithium mining and battery manufacturing.
1. Lithium Mining: Environmental and Social Concerns
Lithium is a critical component of lithium-ion batteries, but its extraction can have serious environmental and social consequences.
- Water Usage: Lithium mining, particularly in arid regions like the Atacama Desert in Chile, requires large amounts of water. This can deplete local water resources, affecting ecosystems and communities that rely on them.
- Habitat Destruction: Mining activities can lead to habitat destruction and biodiversity loss. The extraction of lithium and other raw materials, such as cobalt and nickel, often involves clearing large areas of land, disrupting local ecosystems.
- Chemical Pollution: The extraction and processing of lithium can result in chemical pollution, including the release of toxic substances into the air, water, and soil. This can have long-term impacts on environmental and human health.
- Social and Ethical Issues: Lithium mining has raised concerns about labor practices and human rights violations, particularly in countries like the Democratic Republic of Congo, where cobalt is mined. Ensuring ethical sourcing and supply chain transparency is critical for addressing these issues.
2. Battery Manufacturing: Energy-Intensive Processes
The production of lithium-ion batteries is energy-intensive and can generate significant greenhouse gas emissions.
- Raw Material Extraction: The extraction of raw materials such as lithium, cobalt, and nickel involves energy-intensive processes that contribute to carbon emissions. The transportation of these materials to manufacturing facilities further adds to the carbon footprint.
- Manufacturing Emissions: The production of battery cells and packs involves high-temperature processes and the use of chemicals, which can generate emissions and waste. The energy required for these processes often comes from fossil fuels, particularly in regions where renewable energy is not widely available.
- Supply Chain Complexity: The global supply chain for battery production is complex, involving multiple stages and stakeholders. This complexity can make it challenging to monitor and reduce the environmental impact of battery manufacturing.
Advancements in Sustainable Battery Production and Recycling
Despite the environmental challenges associated with battery production, significant advancements are being made to improve sustainability and reduce the environmental impact of lithium-ion batteries.
1. Sustainable Mining Practices
Efforts are underway to develop more sustainable mining practices that minimize environmental and social impacts.
- Water Conservation: Innovations in water recycling and conservation are helping to reduce the water footprint of lithium mining. For example, some mining operations are implementing closed-loop water systems to minimize water usage and prevent contamination.
- Habitat Restoration: Mining companies are increasingly adopting practices to restore habitats and biodiversity after mining activities. This includes reforestation, soil remediation, and the creation of protected areas.
- Ethical Sourcing: Initiatives such as the Responsible Cobalt Initiative and the Global Battery Alliance are working to improve transparency and ethical practices in the mining of raw materials. These efforts aim to ensure that mining activities do not violate human rights or harm local communities.
2. Green Manufacturing
The battery manufacturing industry is adopting greener practices to reduce emissions and waste.
- Renewable Energy: Many battery manufacturers are transitioning to renewable energy sources, such as wind and solar, to power their production facilities. This reduces the carbon footprint of battery manufacturing and supports the transition to a low-carbon economy.
- Energy Efficiency: Advances in manufacturing technology are improving energy efficiency and reducing emissions. For example, some manufacturers are using energy-efficient kilns and reducing the use of harmful chemicals in the production process.
- Circular Economy: The adoption of circular economy principles is helping to minimize waste and maximize resource efficiency. This includes designing batteries for easier disassembly and recycling, as well as implementing take-back programs for used batteries.
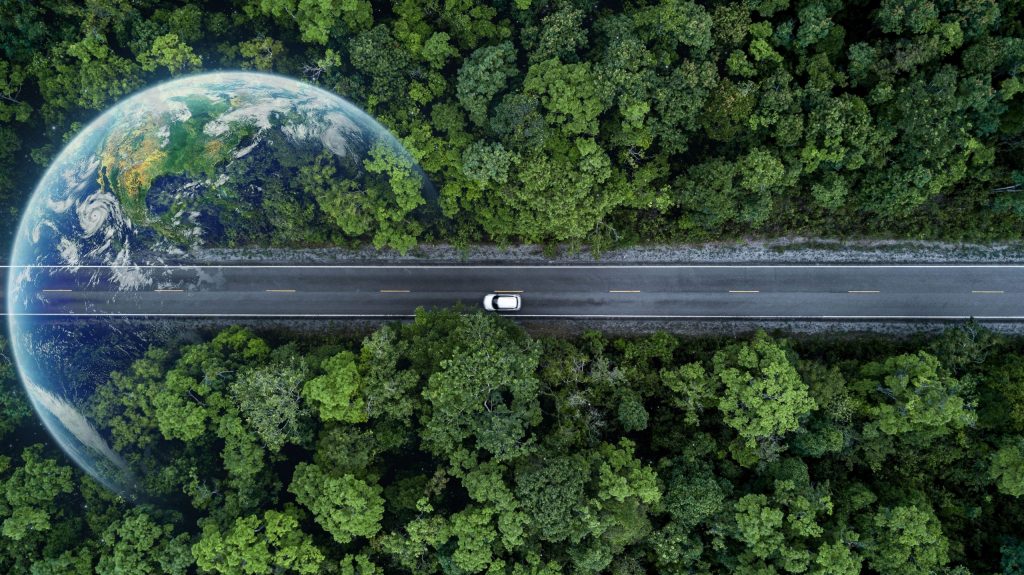
3. Battery Recycling and Second-Life Applications
Battery recycling and second-life applications are critical for reducing the environmental impact of lithium-ion batteries.
- Closed-Loop Recycling: Closed-loop recycling systems recover valuable materials from used batteries, such as lithium, cobalt, and nickel, and reuse them in new batteries. This reduces the need for new mining and minimizes waste.
- Second-Life Applications: Used EV batteries that no longer meet the performance requirements for vehicles can be repurposed for other applications, such as energy storage for renewable energy systems. This extends the lifespan of the batteries and reduces the demand for new battery production.
- Recycling Technology: Advances in recycling technology are improving the efficiency and cost-effectiveness of battery recycling. For example, hydrometallurgical processes use water-based solutions to extract metals from used batteries, reducing the environmental impact compared to traditional pyrometallurgical methods.
Comparing the Carbon Footprint of EVs and ICE Vehicles
To fully understand the environmental impact of EVs, it is essential to compare their carbon footprint to that of ICE vehicles over their entire lifespan.
1. Manufacturing Phase
The production of EVs, particularly the batteries, generates more emissions than the production of ICE vehicles. However, this difference is offset by the lower emissions during the operational phase of EVs.
- EV Manufacturing: The production of lithium-ion batteries is energy-intensive and generates significant emissions. However, advancements in manufacturing technology and the use of renewable energy are helping to reduce these emissions.
- ICE Vehicle Manufacturing: The production of ICE vehicles also generates emissions, particularly from the manufacturing of engines and exhaust systems. However, the emissions from ICE vehicle production are generally lower than those from EV production.
2. Operational Phase
The operational phase is where EVs have a significant advantage over ICE vehicles in terms of emissions.
- EV Emissions: EVs produce zero tailpipe emissions and are more energy-efficient than ICE vehicles. The emissions associated with charging EVs depend on the energy mix of the electricity grid. In regions where electricity is generated primarily from renewable sources, the carbon footprint of EVs is minimal.
- ICE Vehicle Emissions: ICE vehicles emit CO2, NOx, and PM directly from their tailpipes. These emissions contribute to climate change and air pollution, particularly in urban areas.
3. End-of-Life Phase
The end-of-life phase of vehicles involves the disposal and recycling of components, which can have environmental impacts.
- EV End-of-Life: The disposal and recycling of EV batteries can generate emissions, but advancements in recycling technology are helping to mitigate these effects. Recycling batteries can recover valuable materials and reduce the need for new mining.
- ICE Vehicle End-of-Life: The disposal of ICE vehicles also generates emissions, particularly from the recycling of metals and the disposal of hazardous materials such as engine oil and coolant.
4. Overall Carbon Footprint
When considering the entire lifecycle, EVs generally have a lower carbon footprint than ICE vehicles, particularly in regions where electricity is generated from renewable sources. The lower emissions during the operational phase of EVs more than offset the higher emissions during the manufacturing phase.
Conclusion
While the production of lithium-ion batteries for electric vehicles presents environmental challenges, significant advancements are being made to improve sustainability and reduce the environmental impact of battery production and recycling. When considering the entire lifecycle, EVs generally have a lower carbon footprint than ICE vehicles, particularly in regions where electricity is generated from renewable sources. By adopting sustainable mining practices, green manufacturing, and advanced recycling technologies, the EV industry can maximize its environmental benefits and contribute to a cleaner, greener future. The transition to electric mobility is a critical step in addressing the environmental challenges of our time, and the ongoing advancements in battery technology and sustainability are helping to ensure that EVs are truly a cleaner alternative to traditional vehicles.