Introduction: The Shift from Combustion Engine Vehicles to Electric Vehicles
The automotive industry is undergoing a seismic shift, transitioning from combustion engine vehicles (ICEVs) to electric vehicles (EVs). This transition is not only driven by a growing demand for more sustainable transportation options but also by technological advancements and environmental concerns. Governments, consumers, and automakers alike are increasingly prioritizing the benefits of EVs, such as lower carbon emissions, reduced air pollution, and the shift toward renewable energy sources.
However, this transition is far from simple. It poses several challenges for manufacturers accustomed to producing traditional gasoline and diesel-powered vehicles. While the benefits of EV adoption are undeniable, automakers face complex obstacles as they move from internal combustion engines to electric drivetrains. These challenges are compounded by supply chain considerations, the need for new production methods, and the constant evolution of electric vehicle technology.
In this article, we will explore the advantages and challenges faced by manufacturers in their transition from traditional combustion engine vehicles to electric vehicles. Through examining the technological, economic, and regulatory aspects of this transition, we will determine if the advantages of EVs can overcome the hurdles posed by traditional manufacturing processes.
The Advantages of Electric Vehicle Manufacturing
1. Simplified Vehicle Design and Production
One of the most significant advantages of electric vehicle manufacturing is the simplified vehicle design and production process. Compared to internal combustion engines (ICE), electric drivetrains consist of fewer moving parts, which can lead to more efficient and cost-effective production.
Electric vehicles require far fewer components than traditional vehicles. For example, they do not need a complex transmission, exhaust system, or fuel system. The absence of these parts reduces assembly time and the associated costs. Manufacturers can streamline production, leading to greater economies of scale in the long run. Moreover, EVs also do not require oil changes or maintenance related to the engine, contributing to lower overall costs for consumers and manufacturers alike.
2. Lower Maintenance Costs and Longer Lifespan
Electric vehicles are known for their durability and reduced maintenance needs. Because they do not rely on complex internal combustion engine components, EVs typically experience fewer breakdowns. The key components in an EV – the electric motor and the battery – have fewer moving parts compared to the components of a traditional car, which results in reduced wear and tear.
This characteristic reduces maintenance costs for both manufacturers and consumers. Additionally, the absence of a combustion engine means that EVs are quieter and produce less heat, further enhancing their longevity. Manufacturers can leverage this feature to appeal to environmentally-conscious consumers looking for vehicles with lower life-cycle costs.
3. Environmental Sustainability and Green Manufacturing
Electric vehicles provide a significant advantage in terms of environmental sustainability. As the global automotive industry moves toward a low-carbon future, manufacturers are under increasing pressure to reduce the environmental impact of their production processes. EVs contribute to the reduction of greenhouse gas emissions, both during the production process and throughout the vehicle’s lifespan.
Many automakers are also adopting greener production methods, such as using renewable energy sources in manufacturing plants, reducing waste, and recycling materials. By transitioning to EV production, automakers can reduce their carbon footprint and improve their public image, aligning with global sustainability goals.
The Challenges of Electric Vehicle Manufacturing
Despite the advantages, the shift to electric vehicle manufacturing presents several challenges for automakers. These challenges span from technological limitations to supply chain disruptions, and even cultural resistance within organizations. While some manufacturers are making strides, these obstacles must be overcome if the transition is to be successful.
1. Battery Production and Supply Chain Issues
A significant obstacle in the transition to electric vehicles is the production of high-quality, cost-efficient batteries. EV batteries are the most expensive component of an electric vehicle, representing a substantial portion of the overall cost of the vehicle. Battery technology, specifically lithium-ion batteries, has improved significantly over the years, but it remains a complex and costly area of development.
Battery production requires a reliable supply of raw materials such as lithium, cobalt, and nickel. These materials are often sourced from regions with limited infrastructure, political instability, or environmental concerns. As demand for EVs grows, manufacturers face increasing pressure to secure these materials and develop more efficient ways to produce batteries. Supply chain disruptions or shortages of critical materials can slow down the entire EV production process, limiting the growth potential of manufacturers.
2. Charging Infrastructure and Energy Demands
While electric vehicles themselves may be simpler to produce, the infrastructure required to support them presents a significant challenge. EVs rely on charging stations, which need to be widespread and easily accessible for consumers to fully embrace the technology. In many parts of the world, the charging infrastructure remains underdeveloped.
For manufacturers, investing in charging infrastructure presents both a challenge and an opportunity. Some companies, like Tesla, have taken the lead by creating their own proprietary charging networks, but many automakers are still dependent on third-party providers to expand their networks. In addition, the demand for electricity to power the charging stations is rising, putting pressure on local utilities to ensure that the energy supply is stable and sustainable.
3. The Need for New Manufacturing Processes and Equipment
The transition to electric vehicles requires manufacturers to adopt new production methods and equip their factories with cutting-edge machinery. Many traditional auto manufacturers are finding themselves having to retool their existing production lines or build entirely new factories dedicated to EV production.
Electric vehicles require specialized assembly lines for the installation of batteries, electric motors, and high-voltage wiring. Traditional car manufacturers that rely on ICE vehicle production face the significant challenge of reconfiguring their facilities to accommodate these new processes. Retrofitting or building new plants requires significant capital investment, and the pace of EV adoption may not be sufficient to offset these costs in the short term.
4. Workforce Retraining and Skill Gaps
The shift from internal combustion engines to electric drivetrains requires a workforce with new skills. Automotive workers who have spent years or decades working on the assembly of ICE vehicles may not have the necessary skills to work on electric vehicles. Manufacturers must invest in workforce retraining programs to ensure that their employees are capable of handling the new technology.
In addition, EV production requires expertise in areas like battery technology, electrical systems, and software development. Many manufacturers are struggling to fill these specialized roles, leading to a skills gap in the industry. Competing for talent in this high-demand field is another significant challenge for automakers as they try to accelerate their transition to EV production.
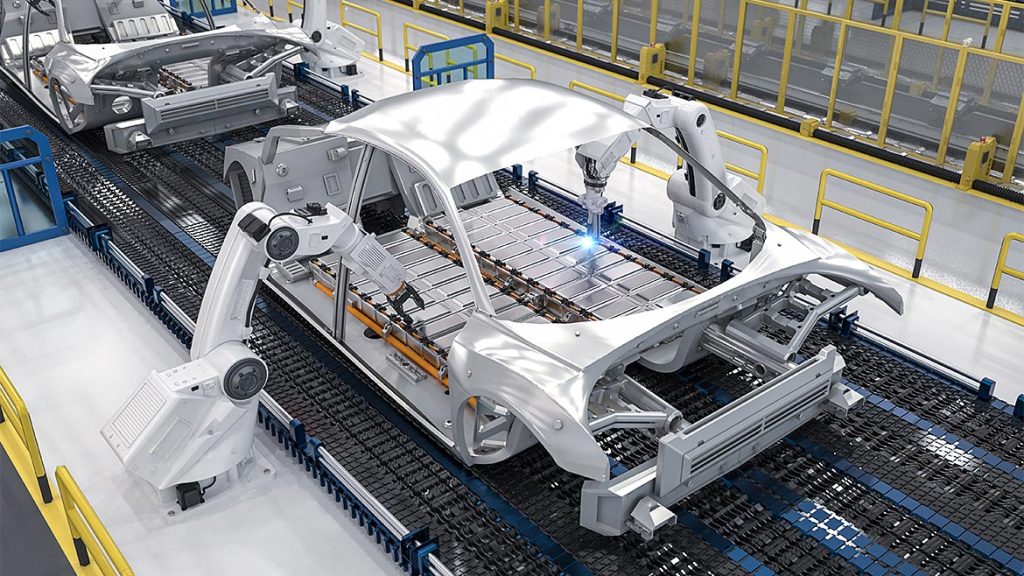
5. Cost Competitiveness and Consumer Adoption
While the advantages of electric vehicles are clear, cost competitiveness remains an obstacle to widespread adoption. Electric vehicles are still more expensive to produce than their ICE counterparts, largely due to the high cost of batteries. Although battery prices have been decreasing steadily, EVs still represent a significant financial investment for consumers.
In many markets, the higher upfront cost of EVs continues to be a barrier to adoption, despite the long-term savings on fuel and maintenance. Manufacturers need to find ways to reduce production costs and make EVs more affordable for a broader range of consumers. This will likely require continued advancements in battery technology, greater economies of scale in production, and possibly government incentives to offset the higher costs.
Overcoming the Challenges: The Path Forward
Despite the significant challenges, the transition to electric vehicle manufacturing is not only possible but also essential for the future of the automotive industry. To successfully navigate these obstacles, manufacturers must adopt a multi-pronged approach that includes technological innovation, strategic partnerships, and long-term investments in infrastructure and workforce development.
1. Technological Innovation in Battery Production
Advancements in battery technology are essential to reducing costs and improving the performance of electric vehicles. Manufacturers must continue to invest in research and development to create more efficient and affordable batteries. New battery chemistries, such as solid-state batteries, hold promise for significantly improving energy density and reducing costs.
Moreover, manufacturers should explore alternative materials for battery production, reducing reliance on scarce or geopolitically sensitive resources. By investing in battery recycling and second-life applications, automakers can also contribute to the circular economy and reduce the environmental impact of battery production.
2. Collaboration with Charging Infrastructure Providers
Building a robust charging infrastructure will require collaboration between automakers, energy companies, and governments. By working together, these stakeholders can ensure that EV charging stations are accessible, reliable, and cost-effective. Governments must also play a crucial role by implementing policies that incentivize the development of public and private charging networks.
3. Workforce Investment and Reskilling
To address the skills gap in EV production, automakers must invest in workforce development programs that focus on new technologies. Partnerships with universities and technical colleges can help prepare the next generation of workers for careers in electric vehicle manufacturing, battery technology, and software development.
4. Government Support and Incentives
Governments play a key role in supporting the transition to electric vehicles by providing subsidies, tax incentives, and grants to both manufacturers and consumers. These incentives can help reduce the financial burden on both parties and accelerate the adoption of electric vehicles.
Conclusion: A New Era of Automotive Manufacturing
The shift to electric vehicles represents a profound transformation for the automotive industry. While the transition presents significant challenges, including battery production, charging infrastructure, workforce retraining, and cost competitiveness, the long-term benefits of EV adoption are undeniable. As manufacturers adapt their production processes and invest in new technologies, they will overcome these obstacles and help shape a sustainable, low-carbon future for transportation.
The future of electric vehicle manufacturing is bright, but success will depend on how well automakers can navigate the complexities of this transition. By leveraging technological innovation, strategic partnerships, and workforce development, the automotive industry can pave the way for a cleaner, more sustainable future.